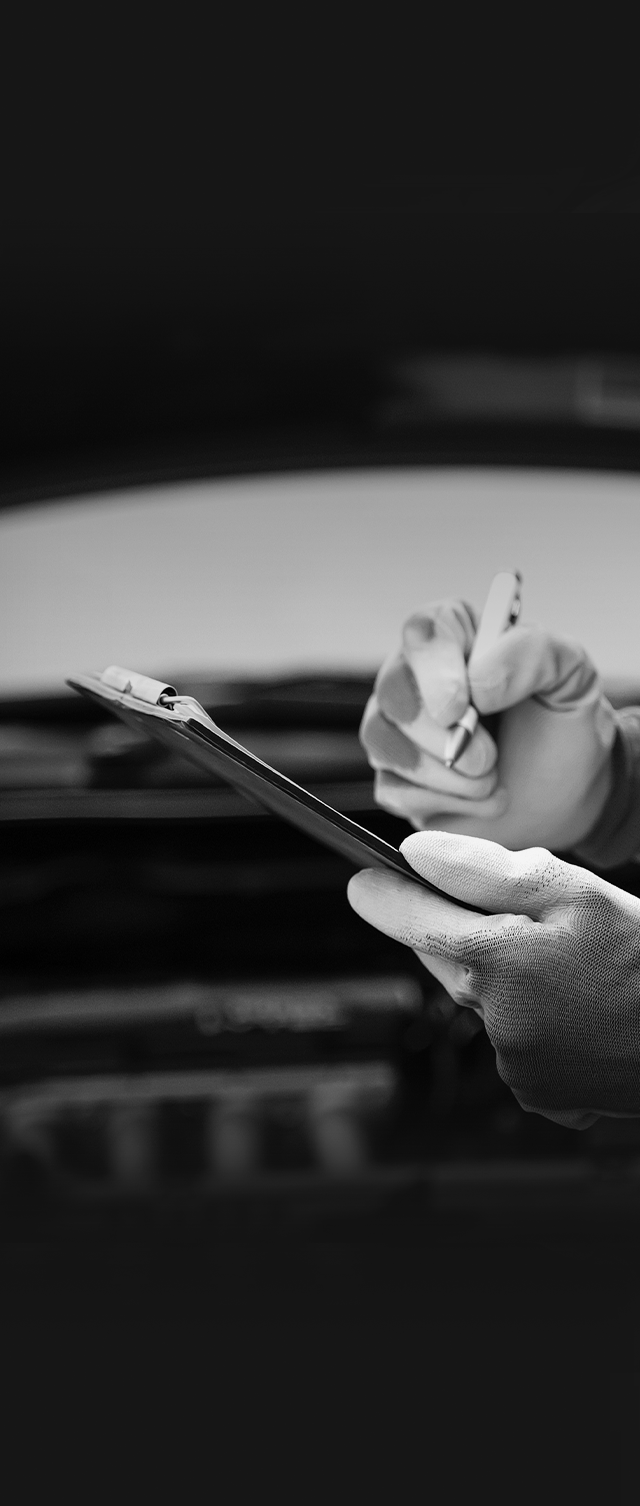
3D printing for car service centers
MJF technology will expand the set of engineering advantages and optimize the production processes of your auto repair shop.
Use it to realize the most daring ideas and projects.
Using 3D scanners, we recreate models of injection molds, tools, metal structures, individual car parts, and decorative items and print them.
How MJF technology is used by car services
-
3D printing of automotive components, parts and mechanisms
Print unique, rare, and discontinued car parts.
The parts are made on the Hewlett Packard Jet Fusion 5210 industrial 3D printing line from HP PA 12 polymer, polypropylene (PP), and thermoplastic polyurethane (TPU).
The finished product does not require post-processing or painting. -
Prototype printing and functional testing
Prototype and test products before mass production.
HP Jet Fusion technology enables you to print part-to-part, hinged joints, and 3D models of any complexity.
Prints take less than a week to complete, allowing you to quickly produce a part, test its performance, and refine the prototype model as needed.
Advantages of 3D printing
-
01
Faster than casting
There is no need to wait months for a mold to be made. Printing with MJF technology takes only a few days. This allows you to quickly create a prototype in the shortest possible time.
-
02
Quick time to market
Fast time to market It’s difficult to create an accurate mold the first time. Thanks to 3D printing, the product can be quickly tested and the 3D model can be modified if necessary without financial risks or missed deadlines.
-
03
Complex shapes
An industrial 3D printing line can print products with complex shapes, such as nested structures, hinged joints, and even chains. The finished parts do not need to be glued or soldered, so the products will be seamless. Casting cannot cope with such tasks.
-
04
Payback on volumes of up to 1000 products
3D printing is a profitable alternative to casting for small-scale production. The customer does not have to invest heavily in the production of a mold, which makes it possible to make a profit after the first batch of printing.
-
05
Advantages of complex geometry
MJF technology offers many design possibilities – you can print products with a porous, perforated, or corrugated surface. The finished structures will be lightweight and durable at the same time.
-
06
It helps to know the demand
Check the need for products before mass production. Print a small batch of products and find out how interesting the product is to customers.
-
07
Customization and further processing
At the customer’s request, printed products can be branded: a unique inscription, logo, and QR code can be placed on them. Finished parts can be easily refined by polishing and painting.
-
08
Convenient product development
One printing cycle takes 3-5 days, which is very convenient when developing a prototype. The product can be tested, the 3D model finalized, and printed again with the corrections. This does not require a lot of time or large financial costs.
Frequently asked questions
-
How long does it take you to fulfill orders?
A printing cycle takes 3–5 days. It includes building, cooling, and sandblasting.
-
What materials do you use for prototype building?
We print products from Hewlett-Packard proprietary materials: HP PA 12 polyamide, polypropylene (PP), and thermoplastic polyurethane (TPU). All of them are stronger and more chemically resistant than ABS and photopolymers.
ABS plastic melts at a temperature of 105°C. The melting point for HP PA 12 is 187°C, for PP it is 138°C, and for TPU it is 192°C. All of these materials are resistant to stress, vibration, chemicals, and water. They are used in the automotive, industrial, medical, and other fields.
The strength of the product depends not only on the material but also on the thickness of its walls. Follow our guidelines on how to prepare models from HP PA 12, PP, and TPU for printing to obtain the best results.
-
What are the maximum dimensions?
The printer has a build area of 380 × 284 × 380 mm.
If the model is larger than that, it is divided into parts and then assembled. This is how car bumpers and dashboards, architectural models, and sculptures are created. Our online calculator doesn’t divide models into parts, so only project managers can adequately assess the build price in such cases.
Send your oversized models to our manager:
Tel.: +38 (099) 075 59 95Telegram: https://t.me/infomir3dprinting
Email: 3dprint@infomir.com
-
How precise is MJF printing?
The HP Jet Fusion 5210 applies polymer in layers of 0.08 mm with a horizontal resolution of 1,200 × 1,200 DPI and a margin of error of 0.08–0.1 mm.
The horizontal resolution is based on the maximum precision of the X- and Y-axis movement of the printhead. The higher the number, the higher the level of detail. Vertical resolution is the minimum thickness of the polymer layer applied in one pass. The thinner the layer, the smoother the build’s surface is.
-
Do you do post-processing?
The completed builds only undergo sandblasting to remove surplus polymer. Optionally, they can also be colored.
We use two coloring methods:
- Dyeing. The application of color by immersing the item into a reservoir of dye.
- Graphite blasting. Similar to sandblasting, but with glass and graphite as an abrasive material. It gives the item a dark-gray color.
Dyeing and blasting are inexpensive and efficient ways of getting a high-quality finish.
Available colors: graphite, black, and gray. Other finishes will soon be made available. -
How do I pay for my order?
You can pay for your order once our manager clarifies all the details with you. Infomir 3D Printing fulfills orders only on pre-paid terms. You can pay for your order with a cashless payment.
For cashless payments, we need the client to submit their registration certificate, VAT payer’s certificate, and banking details. After the order is paid for, we will deliver the finished items together with an invoice.
-
Do you provide 3D scanning/modeling services?
Our specialists work with finished models. If you need a model developed or 3D scanned, we can refer you to our trusted partners.
Frequently asked questions
-
What chemicals can TPU withstand?
TPU exhibits good resistance to a variety of chemical agents, including oils, solvents, and some acids, making it suitable for use in environments where chemical resistance is required.
-
What are the advantages of using TPU in the creation of functional parts?
Using TPU allows for the production of items that are highly wear-resistant, withstand mechanical stresses, and are durable. This makes TPU an ideal choice for manufacturing functional parts in high-stress and demanding environments.
-
In which industries is TPU used?
TPU is widely used in the automotive industry, medicine, footwear manufacturing, and other industrial areas. For example, it is used to make flexible and durable components such as seals and flexible tubes in the automotive industry, orthotic insoles and prostheses in medicine, and comfortable insoles and soles in the footwear industry.
-
What is TPU and what are its features for 3D printing?
TPU (thermoplastic polyurethane) is a powder used in industrial 3D printers like the HP Jet Fusion 5210 to create products that are highly resilient, durable, and chemically resistant. The material allows for the stiffness of products to be adjusted, making it a versatile choice for many industries.
-
How does polypropylene PP differ from polyamide HP PA 12?
Polyamide and polypropylene have many common physical properties, but there are also some differences, as provided below.
- The melting point of PA 12 powder is 187°C, and that of PP is 138°C.
- The bulk density of PA 12 powder is 1.01 g/cm³, and that of PP is 0.34 g/cm³ (polypropylene products are lighter than polyamide ones).
- The hardness (Shore D) of polyamide is 80, and that of polypropylene is 68 (products made of polyamide are stronger).
More details about polyamide and polypropylene can be found in the corresponding comparison table.
-
How does thermoplastic polyurethane TPU differ from polyamide HP PA 12?
Polyamide and thermoplastic polyurethane react equally to exposure to chemicals, moisture, and radiation. There are many common physical properties, but there are also some differences, as provided below.
- The melting point of PA 12 powder is 187°C, and that of TPU is 192°C.
- The particle size of PA 12 powder is 60 microns, and that of TPU is 100 microns (the printing resolution of polyamide is higher, so more detailed products can be printed from it).
- Only solid products that do not change shape can be printed from polyamide. The properties of TPU make it possible to create flexible products and adjust the degree of their flexibility depending on the customer’s needs.
More details about polyamide and thermoplastic polyurethane can be found in the corresponding comparison table.
-
What does a demo box include?
The set includes items from different 5 industries.
We regularly update the demo set. It always includes 7–10 items for different applications:
Prototypes
Working samples of parts and finished items with a high-quality surface finish.
Device enclosures/casings
Multi-part enclosures or casings for electronic devices for fit-up assembly.
Mechanism parts
Working parts of mechanisms, e.g., cogs, mounts, tubes, and pivot joints.
Medical items
Models of joints, jaws, and other organs, respirators, ventilator adapters, and other medical items.
Figurines and keyringsSouvenirs, character figurines, keyrings with detailed logos, inscriptions, and surface quality rivaling that of cast products.
Find out more: Printed samples
-
What is a demo box?
Our demo box is a set of items printed with Multi Jet Fusion technology. It includes prototypes, enclosures and casings, moving parts, anatomic models, figurines, and keyrings.
The parts are made of HP PA 12 polyamide, polypropylene (PP) and thermoplastic polyurethane (TPU). You can check their durability, porousness, as well as their resistance to water, and low and high temperatures. The demo box will help you decide if Multi Jet Fusion technology is the right fit for your project.
-
How can I get samples?
At the end of each tour, visitors receive a demo set of printed items, including enclosures, prototypes, mechanism parts, figurines, and souvenirs. You will be able to check those out yourself and show them to colleagues at your company.
You can get a demo box even without visiting our facility—simply send a request for one on our demo sample page.
-
How long does it take you to fulfill orders?
A printing cycle takes 3–5 days. It includes building, cooling, and sandblasting.
-
What materials do you use for prototype building?
We print products from Hewlett-Packard proprietary materials: HP PA 12 polyamide, polypropylene (PP), and thermoplastic polyurethane (TPU). All of them are stronger and more chemically resistant than ABS and photopolymers.
ABS plastic melts at a temperature of 105°C. The melting point for HP PA 12 is 187°C, for PP it is 138°C, and for TPU it is 192°C. All of these materials are resistant to stress, vibration, chemicals, and water. They are used in the automotive, industrial, medical, and other fields.
The strength of the product depends not only on the material but also on the thickness of its walls. Follow our guidelines on how to prepare models from HP PA 12, PP, and TPU for printing to obtain the best results.
-
What safety certificates does the PA 12 material have?
We guarantee that our printer’s output is safe. The PA 12 polyamide contains no heavy metals, phthalates, and bisphenol A, meaning that it’s safe enough even for toys.
Besides, it meets all European and American biocompatibility and fire safety requirements.
-
What material do you use for 3D printing?
Three materials are used for printing on the HP Jet Fusion 5210 line: HP PA 12 polyamide, polypropylene (PP), and thermoplastic polyurethane (TPU).
HP PA 12 can withstand physical stress and vibration and is resistant to low and high temperatures; products retain their properties and shape under temperature exposure ranging from −50°C to 150°C. The melting point of HP PA 12 is 187°C (for comparison, for ABS plastic, this value is 105°C). This material is used in the automotive and aerospace industries. For more details about the PA 12 polyamide, see the Hewlett Packard document.
PP is the optimal solution for printing lightweight products that are resistant to chemical exposure and water. The bulk density of polypropylene powder is 0.34 g/cm³, which is almost three times less than that of polyamide (1.01 g/cm³). Due to that, polypropylene products are lightweight. The material is suitable for printing device cases, automotive parts, prototypes, etc.
TPU is a material that allows you to print flexible products (flexibility can be adjusted depending on the customer’s tasks). Thermoplastic polyurethane is also moisture- and chemical-resistant, with a powder melting point of 192°C. This material is used in the light and automotive industries, medicine, electronics, and other fields.
When choosing a material, please be aware that the strength of the product depends on its design features and the thickness of its walls. Follow our guidelines on how to prepare models from PP, HP PA 12, and TPU for printing to develop the optimal product model.
-
How fast does HP Jet Fusion 5210 print?
At full capacity, printing takes no more than 12.5 hours. If the building volume is only partially filled, the printing time becomes proportionately shorter.
The build cannot be removed from the station immediately after its completion, as the material’s mechanical properties will suffer from flash cooling. In Fast Cooling mode, it takes 4 hours for the build to cool entirely, and in Natural Cooling mode it takes up to 30 hours. Cooling is done in a separate module, so it has no impact on the printing performance. -
How precise is MJF printing?
The HP Jet Fusion 5210 applies polymer in layers of 0.08 mm with a horizontal resolution of 1,200 × 1,200 DPI and a margin of error of 0.08–0.1 mm.
The horizontal resolution is based on the maximum precision of the X- and Y-axis movement of the printhead. The higher the number, the higher the level of detail. Vertical resolution is the minimum thickness of the polymer layer applied in one pass. The thinner the layer, the smoother the build’s surface is.
-
What color will the build have?
Multi Jet Fusion produces items gray in color. This is what polyamide powder looks like in finished builds.
However, we can also change the color of the printed item should the client require it. We currently offer two colors: black and graphite. To learn more about coloring, follow this link or contact our manager.
-
What kind of dust and moisture protection will the builds have?
We use several types of materials for printing.
The properties of HP PA 12 polyamide make it possible to create device cases and parts with an IP67 rating for dust and water protection. Finished products are not harmed by contact with fine dust. Physical properties are preserved when in contact with rain, running water, or sea waves. Products made of this material withstand a 30-minute immersion in water to a depth of 1 meter. Due to the high density of the polymer, such products do not absorb water and retain their dimensions in a humid environment.
Because of its non-porous structure, polypropylene (PP) is resistant to water, so products made from this material do not require additional treatment with epoxy resins. The water absorption of polypropylene is very low; kept at room temperature for over 6 months, the material absorbs liquids of less than 0.5% of its own weight, and at 60°C, it absorbs less than 2% thereof.
Thermoplastic polyurethane (TPU) also has high water-repellent properties: per 24 hours at 23ºC, the water absorption of the material is 0.6%, the protection level is IP67.
-
Do you do post-processing?
The completed builds only undergo sandblasting to remove surplus polymer. Optionally, they can also be colored.
We use two coloring methods:
- Dyeing. The application of color by immersing the item into a reservoir of dye.
- Graphite blasting. Similar to sandblasting, but with glass and graphite as an abrasive material. It gives the item a dark-gray color.
Dyeing and blasting are inexpensive and efficient ways of getting a high-quality finish.
Available colors: graphite, black, and gray. Other finishes will soon be made available. -
How can the PA 12 items be bonded?
Hewlett Packard recommends the following adhesives for PA 12 bonding:
- Cyanoacrylate (a.k.a. Superglue)
- Loctite 401 and 406
- Epoxy
- Neoprene-based glues
For better bonding reliability, the item’s surface must first be sanded and cleaned.
See Hewlett Packard’s guide to learn more.
-
How is Multi Jet Fusion different from SLS?
Selective Laser Sintering (SLS) and Multi Jet Fusion (MJF) technologies are used for different types of powder 3D printing. Unlike SLS, where the polymer is spot-fused using lasers, MJF fuses the powder and bonding agent with IR light.
For an SLS printer running at 100% capacity, it can take up to 30 hours to fuse and cool the printed product. With MJF, on the other hand, printing takes 12.5 hours, and quick cooling — 4 hours.
Products created using MJF technology have stable mechanical properties and detailed, smooth surfaces. Various materials are used for such printing, as follows:
- Polyamide HP PA 12 allows you to create durable products with complex designs, thin walls, inscriptions, and logos. This material is resistant to water, ultraviolet radiation, and chemicals, as well as being biocompatible.
- Polypropylene is the optimal material for printing prototypes and finished products: car interior elements, cases, boxes, and other items. Polypropylene products are proof against alcohols, oils, ethers, and other chemicals. They are durable and resistant to moisture.
- Thermoplastic polyurethane is suitable for creating flexible elastic products, such as shoe parts, seals, and gaskets. Products made of this material do not crack when deformed and return to their original shape. The material can withstand exposure to oils, solvents, and a number of acids.
Learn more about Multi Jet Fusion technology: https://www.youtube.com/watch?v=sxjsZ5XKmbU
-
What makes HP PA 12 different from ABS and resin?
We print items from Hewlett Packard’s branded polyamide. HP PA 12 is more durable and chemical-resistant than ABS and resins.
ABS melts at 105 °C, whereas HP PA 12 melts at 187 °C. Since the polyamide is also stress and vibration-resistant, it is often used in both the aerospace and automotive industries.
The durability of the final product depends not only on the material but also on the thickness of the structure. For best results, follow our pre-printing model preparation guide.
More details about PA 12 are provided in Hewlett Packard’s specifications. -
What process does HP Jet Fusion 5210 use?
Our 3D printing process includes multiple stages:
1. Visualization
The 3D model is imported into HP SmartStream 3D Build Manager, an app that creates printer tasks. The space outlined in blue is the HP Jet Fusion 5210’s print volume. Its dimensions are 380 × 284 × 380 mm. Once the details are laid out, the app starts preparing the print task.
2. Printer preparation
The build unit is loaded with material and then inserted into the printer. Once this is done, it is ready for launch. Your items will be printed from this polyamide.
3. Printing
The printer applies a layer of powder and bonding agent, which is then fused under IR light. Once the layer is fused, the printing head applies another one. With Hewlett Packard’s solution, a whole layer is fused in one pass.
4. Cooldown
The build should be cooled gradually to preserve the item’s structural properties and prevent the material from becoming brittle. Usually, it takes up to 12 hours for a build to cool down. Meanwhile, the HP Jet Fusion 5210 can print another one. The printer also has active cooling capabilities: the build can be cooled in just 4 hours, but there is no guarantee the material will be as durable.
5. Clean-up
Multi Jet Fusion is a powder printing technology, so the newly built items need to be cleaned from surplus polyamide. All this is done in the post-processing unit.
Once cleaned, the items are ready for use without additional finishing. They can also be dyed black or gray if need be. Then we send them to the customer.
-
Do you provide 3D scanning/modeling services?
Our specialists work with finished models. If you need a model developed or 3D scanned, we can refer you to our trusted partners.
Order 3D printing
-
1. Upload your 3D model
-
2. Specify the quantity and color
-
3. Pay the order
-
4. We print the product
-
5. The order is shipped directly to you